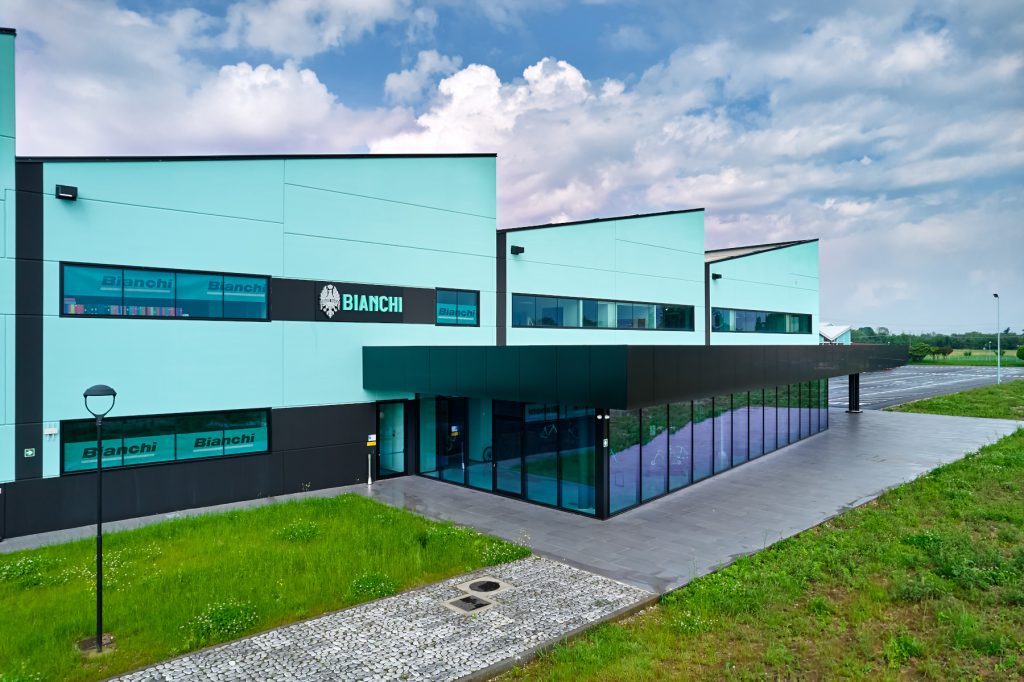
Un nuovo impianto produttivo, tra i primi allineati allo standard industria 5.0 in Italia, utilizza soluzioni eco-compatibili e fonti rinnovabili per garantire ottimali condizioni di comfort e salubrità.
Punto di riferimento nel mondo delle due ruote da oltre 130 anni, Fabbrica Italiana Velocipedi E. Bianchi ha recentemente rinnovato il proprio stabilimento di Treviglio (Bergamo), dedicato alla progettazione e all’assemblaggio di biciclette da passeggio e da gara, mountain bike ed e-bike con pedalata assistita, al top della gamma.
L’ambizioso progetto ha radicalmente trasformato il sito industriale con un nuovo stabilimento a elevato contenuto tecnologico, composto da ambienti concepiti per esaltare il benessere dei lavoratori e caratterizzato da impianti di climatizzazione ad alta efficienza energetica e a bassissimo impatto ambientale.
Innovazione industriale
Inaugurato ufficialmente nel giugno 2024, ma già in funzione da circa un anno, il nuovo edificio produttivo è il primo passo di un articolato programma di rigenerazione del sito industriale che, da oltre 50 anni, ospita la sede e il principale stabilimento dell’azienda.
Caratterizzata dal profilo seghettato degli shed e dall’involucro edilizio colorato con il tipico celeste che distingue da sempre il marchio, la modernissima unità produttiva (superficie totale circa 20.000 m²) ha sostituito il preesistente capannone risalente agli anni ‘70, demolito e ricostruito in tempi da record con soluzioni allo stato dell’arte, per la parte edilizia e impiantistica, ed estremamente innovative, per la parte industriale.
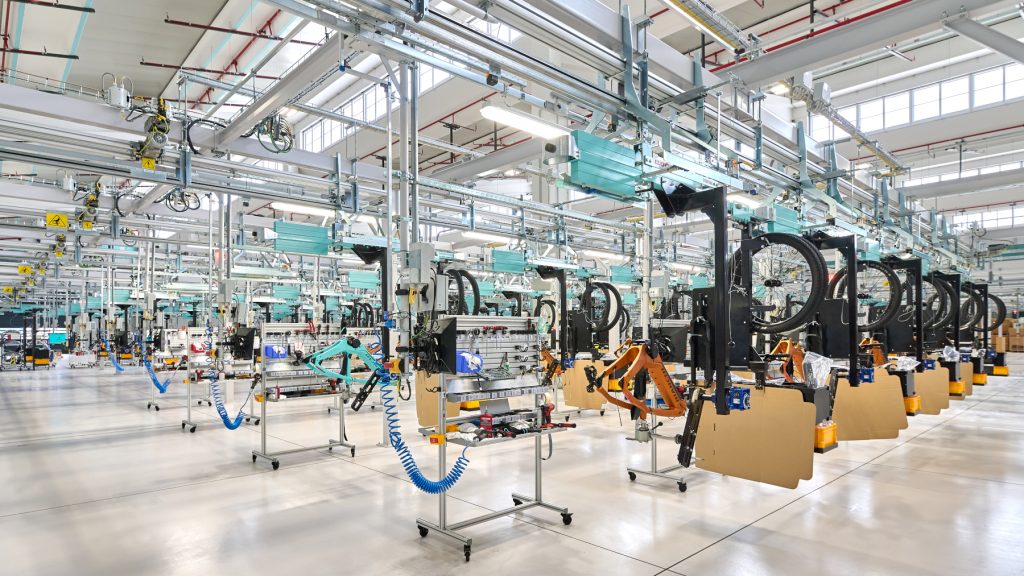
Il progetto ha messo al centro il benessere dei lavoratori, sia con la ridefinizione dell’ergonomia delle postazioni, sia garantendo condizioni di lavoro estremamente confortevoli, fra cui una temperatura interna variabile entro l’intervallo di comfort (20÷26 °C) durante l’arco dell’anno, la ventilazione funzionante in continuo senza creazione di correnti d’aria, l’illuminazione naturale affidata ad ampi lucernari orientati a nord, ecc..
La nuova linea di produzione è una sorta di lean manufacturing progettata ad hoc da Bianchi, per consentire la produzione di 500 biciclette dei più diversi modelli per ciascun turno produttivo. La completa digitalizzazione di ogni postazione d’assemblaggio e l’automazione dell’approvvigionamento delle scorte concorrono al miglioramento della produttività.
Il progetto architettonico è stato sviluppato da Domus ing&arch, con impianti meccanici ed elettrici affidati a T.E.S.I. Engineering. L’impresa Baraclit ha realizzato l’intervento edile con strutture e tamponamenti prefabbricati, collaborando con l’installatore Antonelli Impianti specializzato nell’impiantistica industriale.
In estrema sintesi il nuovo edificio produttivo ospita:
- area produzione (a doppia altezza);
- uffici tecnici, sale riunioni, showroom con esposizione di modelli storici, mensa e locali tecnici (piano terreno);
- reparto corse, uffici amministrativi e dirigenziali, sale meeting e CED, al primo piano.
Oltre al ricorso alla geotermia a ciclo aperto per la climatizzazione, l’edificio dispone anche di superfici fotovoltaiche situate sulle falde degli shed, per una potenza complessiva pari a circa 500 kWp, in grado di garantire la quasi completa autonomia energetica durante il periodo estivo.
Comfort ed efficienza senza compromessi
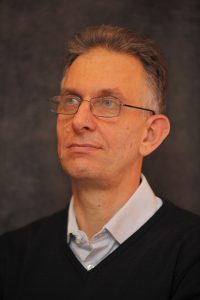
L’ingegner Lorenzo Strauss è fondatore e Presidente di T.E.S.I. Engineering: «Questa commessa è nata sotto i migliori auspici: uno degli obiettivi principali della committenza era realizzare uno stabilimento estremamente confortevole, sotto tutti i punti di vista (termoigrometrico, luminoso/visivo, acustico, ecc.) e in ogni periodo del giorno e dell’anno, in modo da supportare qualsiasi modalità di organizzazione del lavoro.
Le scelte del progetto impiantistico hanno quindi privilegiato una soluzione basata su superfici radianti alimentate da pompe di calore geotermiche, in grado di assicurare la massima stabilità delle condizioni operative e percepite a fronte della minimizzazione dell’impatto energetico e ambientale.
La notevole massa dei pavimenti radianti nell’area produttiva garantisce un’efficacissima stabilità termica, sia dal punto di vista spaziale – in orizzontale e in verticale, poiché elimina praticamente qualsiasi stratificazione – sia dal punto di vista temporale – in virtù dell’elevata inerzia termica del massetto. Questo rende il nuovo stabilimento praticamente insensibile alle variazioni esterne di temperatura (alternanza fra giorno e notte, fenomeni meteorologici, ecc.) e agli apporti termici interni, che non sono trascurabili considerando la potenza elettrica installata per scopi produttivi.
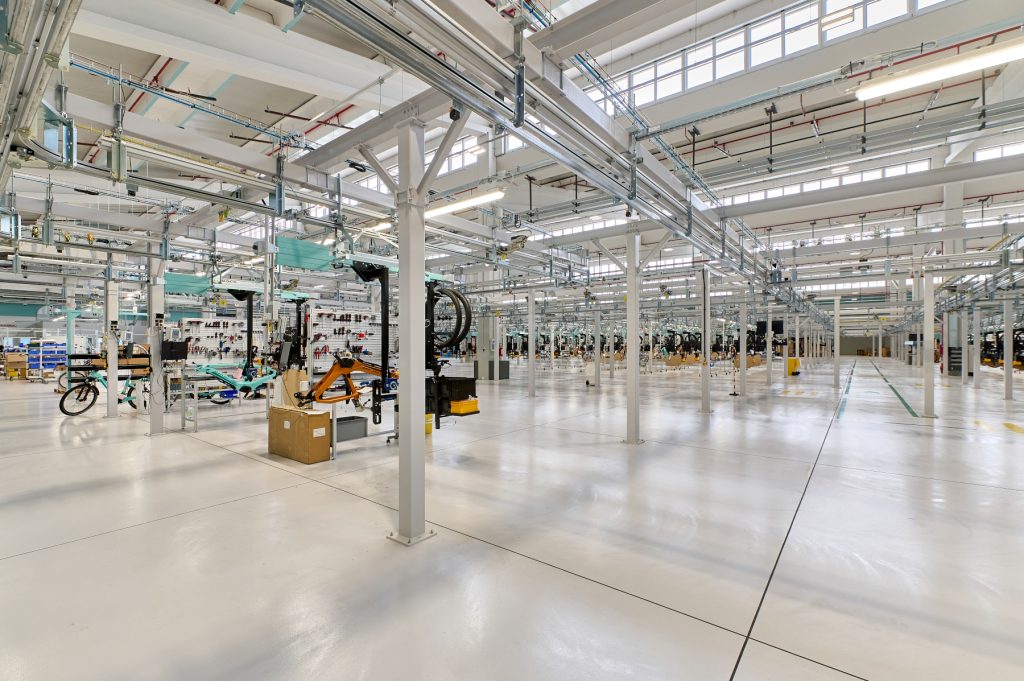
Si tratta di una soluzione ad alto costo d’investimento ma con bassissimi costi di gestione, anche perché dal punto di vista energetico si utilizzano fluidi con temperature moderate. L’assenza di movimenti d’aria e di emissioni acustiche restituisce un ambiente salubre anche dal punto di vista della qualità dell’aria e della riduzione dello stress».
Energia dall’acqua
La produzione dei fluidi termovettori è affidata a pompe di calore che utilizzano l’acqua di falda per lo scambio termico ad alta efficienza energetica. L’acqua è attinta dal sottosuolo (max 180 m³/h) attraverso 2 pozzi (profondità 50 m) dotati di elettropompe centrifughe multistadio sommerse azionate da inverter, con camicia di convogliamento per il raffreddamento a regime di rotazione ridotto, valvole di ritegno a palla e relè di protezione contro la marcia a secco.
La regolazione prevede il controllo di pressione in mandata, con limite minimo di frequenza e pressostato di massima per la commutazione in funzionamento on-off. L’acqua di pozzo è veicolata da tubazioni di polietilene ad alta densità ed è filtrata da cicloni inerziali ad asse verticale, disposti in parallelo, seguiti da un filtro autopulente automatico sempre in esecuzione verticale, con ugelli di pulizia interni al cestello.
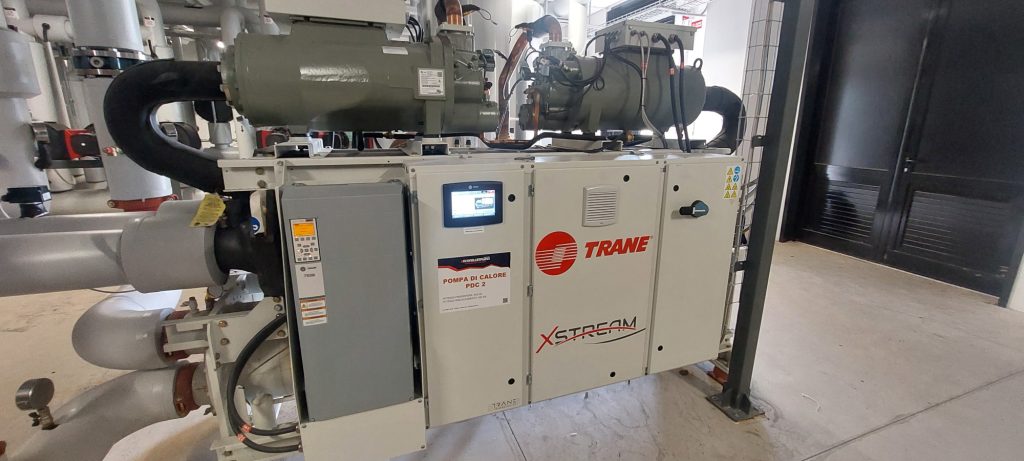
Il trasferimento del calore dal circuito aperto dell’acqua di falda a quello chiuso dei generatori (T ingresso 16 °C; ΔT ±5 °C) è affidato a 3 scambiatori di calore (ciascuno 1.047 kW), situati rispettivamente:
- sul ritorno ai condensatori, per smaltire l’energia termica eventualmente non utilizzata per il riscaldamento (condizione tipicamente estiva);
- sul ritorno agli evaporatori, per consentire l’acquisizione di energia termica per l’insufficiente richiesta dell’impianto di raffreddamento (condizione tipicamente invernale).
- su entrambi i ritorni, a supporto degli scambiatori suddetti, per dimezzare il carico di scambio (quindi lo scarto termico tra primario e secondario) rispettivamente nei periodi estivo e invernale.
Un ulteriore scambiatore di calore (419 kW), posizionato sul ritorno dell’acqua refrigerata, può provvedere al preraffreddamento delle utenze di acqua refrigerata in modalità “natural cooling” (ΔT ±2 °C). L’acqua di falda è infine restituita al terreno attraverso 3 pozzi di resa.
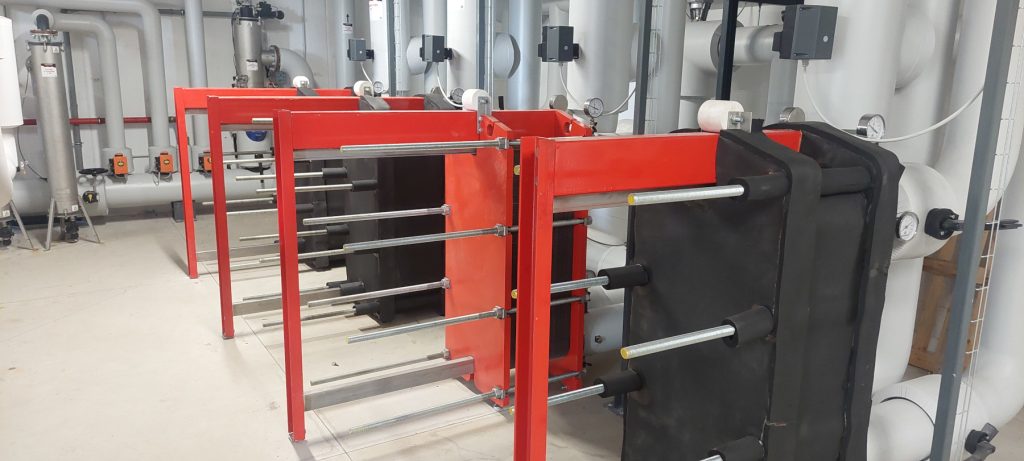
Centrale termofrigorifera
Le due pompe di calore idrotermiche (ciascuna: 365 kWt; 450 kWf) utilizzano R513A e sono equipaggiate con:
- compressori volumetrici rotativi lubrificati a vite, azionati da inverter e completi di valvola a cassetto, modulanti in un range compreso tra 20 e 100%;
- evaporatori e condensatori a fascio tubiero allagato.
I fluidi per la climatizzazione sono prodotti a Tmax = 45 °C (-5 °C) e a Tmin = 6 °C (+5 °C), con commutazione stagionale eseguita sul lato acqua. Nell’esercizio estivo lo scambio di calore diretto tra acqua di pozzo e refrigerata consente in certa misura il natural cooling, con pre-raffreddamento del fluido di ritorno dall’impianto a spese dell’acqua di pozzo.
La circolazione dei fluidi è demandata a elettropompe a portata variabile, del tipo centrifugo monostadio in esecuzione in-line, a rotore bagnato (fino a 50 m³/h) o ventilato (oltre 50 m3/h), con regolazione a pressione differenziale costante o proporzionale gestita dall’elettronica a bordo e dal BMS.
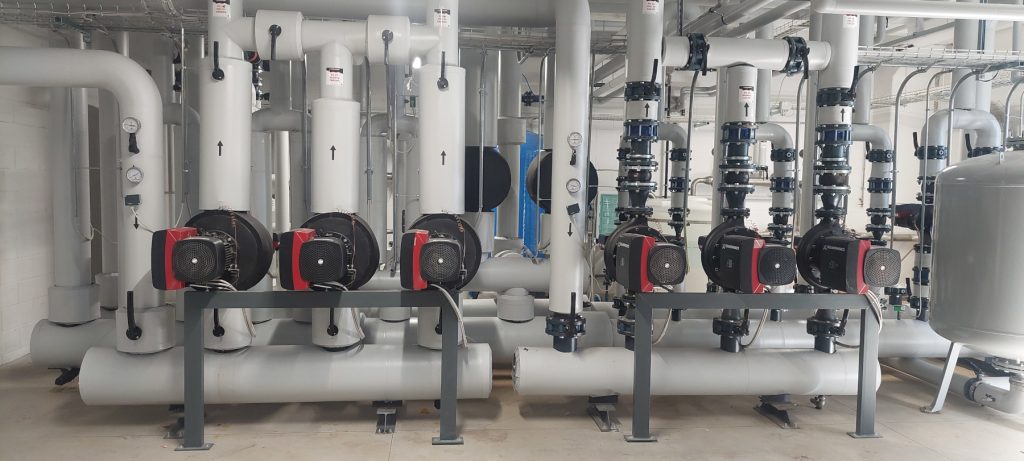
I circuiti primari e secondari sono separati idraulicamente tramite 2 accumuli inerziali (ciascuno 3.000 l), per l’acqua refrigerata e calda (quest’ultimo con serpentino di pre-riscaldamento), con connessione “a 3 tubi” per evitare circolazioni parassite nel serbatoio.
Sono inoltre presenti 2 caldaie a condensazione alimentate a metano (ciascuna 338 kW), del tipo a basamento con bruciatore integrato a irraggiamento con ampio campo di modulazione, per la produzione dell’ACS ed eventuali integrazione e backup della produzione di acqua ad alta temperatura da parte delle pompe di calore, più la predisposizione per un’ulteriore generatore termico.
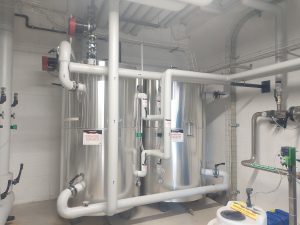
Le caldaie si inseriscono in serie a valle dell’accumulo inerziale, in modo da fornire l’apporto termico direttamente sul collettore di mandata dell’acqua calda, con elettropompe dedicate per l’inseguimento della temperatura di miscela e relativa sonda termica nel collettore.
La rete di distribuzione dell’impianto di climatizzazione è realizzata con tubazioni in acciaio al carbonio, per i rami principali, e in multistrato con posa a pressare, nei tratti terminali, tutte adeguatamente coibentate e protette. Il sistema di compensazione dell’espansione del volume d’acqua è del tipo a pressione costante con vasi chiusi.
Spazi e terminali
Con l’eccezione dei locali tecnici e dei servizi igienici, tutti gli ambienti dello stabilimento sono climatizzati in riscaldamento e raffrescamento, con regolazione autonoma e compensazione della temperatura.
Gli open space produttivi e i locali di supporto (uffici, laboratori, controllo qualità, customer care, attrezzeria e officina, magazzini, ecc.) sono climatizzati da pannelli radianti a pavimento di tipo industriale (spessore medio 20 cm), realizzati con serpentini in tubo di polietilene reticolato (Ø 25 mm, posati a -16 cm dal piano di calpestio con passo di 20 cm).
Le dorsali di distribuzione dei fluidi si diramano verso i collettori di alimentazione, situati in prossimità degli elementi portanti verticali, e quindi alle serpentine annegate nei getti di conglomerato. Il massetto è separato dal terreno sottostante da uno strato termoisolante in polistirene estruso (spessore 4 cm) ad alta resistenza alla compressione, con le singole superfici suddivise da giunti di dilatazione termica.
Nel corpo servizi, uffici e sale riunioni sono equipaggiati con pannelli radianti a soffitto in lastre di cartongesso, alimentati con circuito “a 2 tubi”. In dettaglio, per i locali con terminali radianti sono previste temperature di mandata:
- massima invernale pari a 35 °C (pavimenti) e a 40 °C (controsoffitti);
- minima estiva pari alla temperatura di mandata dell’aria primaria maggiorata di uno scarto impostabile (pavimenti e controsoffitti), con alimentazione alle superfici radianti abilitata solo con l’UTA corrispondente in funzionamento.
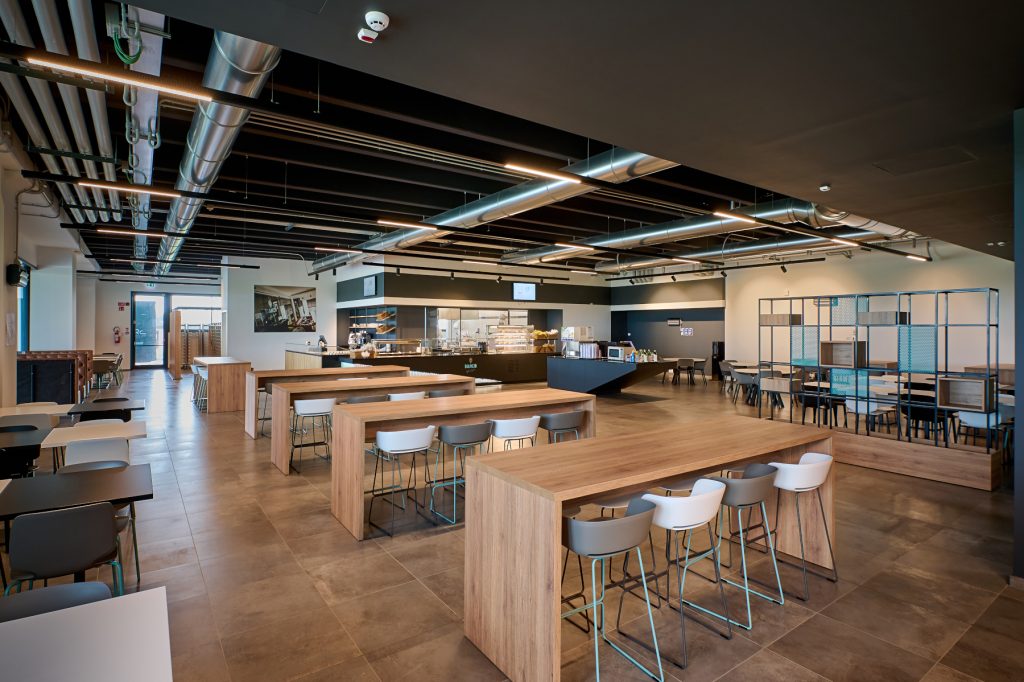
Gli spazi collettivi (mensa, cucina, showroom) e i locali che richiedono un elevato ricambio dell’aria (spogliatoi e servizi igienici) sono dotati di ventilazione a tutt’aria. I locali tecnici con elevati carichi termici (cabina elettrica, CED, UPS, inverter dell’impianto fotovoltaico) utilizzano un sistema di raffrescamento a ventilazione forzata (ventilconvettore alimentato da acqua refrigerata). Nel locale CED, un ulteriore impianto split a espansione diretta si attiva in caso di mancato raggiungimento del set-point.
Reti di ventilazione
Le quattro UTA installate nello stabilimento sono situate nei pressi degli spazi serviti, in locali dedicati o sulla copertura: immettono aria negli ambienti in base a set-point impostabili, indicativamente a 20 °C (periodo invernale, con U.r. 40%) e a 16 °C (periodo estivo). L’UTA dedicata alle aree produttive (mandata 45.000 m3/h) è composta da sezioni per
- presa, mandata, ripresa ed espulsione, opposte e coniugate;
- recupero di calore a flussi incrociati (efficienza 75%), con doppio by-pass (espulsione e presa aria esterna);
- ventilazione con doppi ventilatori a girante aperta, plug-fan, a regime di rotazione variabile;
- pre-filtrazione a pannello e filtrazione a sacco/tasche;
- trattamento termico a doppia batteria;
- umidificazione adiabatica sulla mandata e sull’espulsione (per potenziare il free-cooling).
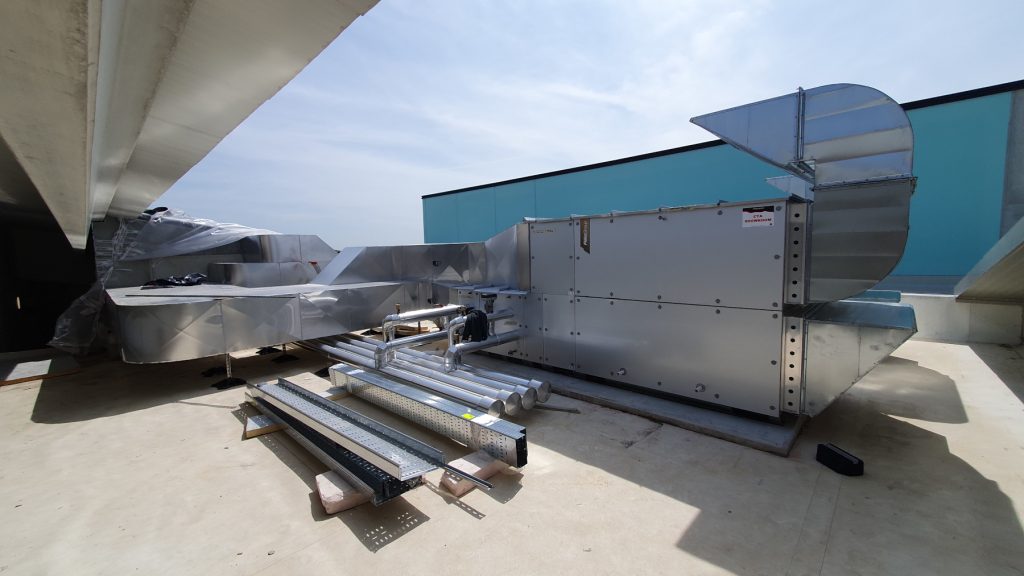
L’aria trattata è distribuita da canalizzazioni con tratti in ambiente in lamiera microforata a sezione circolare, con funzionamento a portata variabile. Il regime pressorio è neutro, in quanto le attrezzature delle linee di assemblaggio dispongono di propri impianti di estrazione e ricircolo compensati.
Le altre UTA alimentano gli impianti:
- ad aria primaria degli uffici e degli altri locali di servizio ai piani terreno e primo (4.900+3.000+14.000 m3/h);
- a tutt’aria degli ambienti collettivi come show-room, mensa e spogliatoi (7.600+4.900+5.100 m3/h);
- a tutt’aria al servizio esclusivo della cucina (14.300 m3/h) in esecuzione multizona, con mandate per la compensazione della cappa pre-riscaldata (da recupero) e con post-riscaldamento dedicato alle aree lavaggio e preparazione;
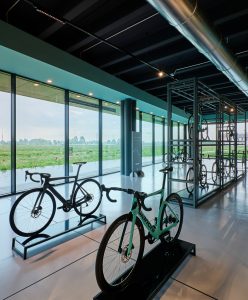
Rispetto a quella dell’area produttiva, queste UTA si distinguono per le sezioni di:
- ricircolo dell’aria, da utilizzare per la sola messa a regime degli ambienti;
- recupero termico dotate di by-pass per free cooling discriminato da comparazione termica tra l’aria ambiente ed esterna, con previsione di strategie di night-cooling;
- ventilazione basata su ventilatori centrifughi a girante libera azionati da inverter, con prevalenza della mandata sull’estrazione, ad eccezione dell’UTA della cucina;
- umidificazione, ad eccezione degli ambienti con elevati carichi latenti.
Altri impianti meccanici
L’acqua potabile è approvvigionata dall’acquedotto ed è sottoposta ad addolcimento e a dosaggio automatico di prodotti disinfettanti e filmanti (per l’uso come ACS). Per mettere sempre a disposizione una temperatura d’erogazione appropriata (set-point impostabile tra 45 e 65 °C) e prevenire qualsiasi proliferazione batterica, la produzione dell’ACS è affidata a:
- pre-riscaldamento istantaneo nell’accumulo inerziale caldo;
- post-riscaldamento con l’acqua tecnica prodotta dalle caldaie.
La preparazione istantanea avviene nei 2 bollitori (ciascuno 2.000 l) completi di serpentino, che utilizzano anche il calore recuperato dal raffreddamento dell’olio dei compressori d’aria grazie a un circuito dedicato. La distribuzione dell’ACS è realizzata con tubazioni in acciaio zincato (rami principali) e multistrato preisolato (tratti terminali).
L’erogazione dell’ACS avviene con circuiti distinti per l’alimentazione diretta della cucina, ad alta temperatura, e la miscelazione termostatica a punto fisso per le altre utenze, a media temperatura. Di conseguenza anche i circuiti di ricircolo sono distinti.
La protezione antincendio del nuovo stabilimento comprende impianti di spegnimento:
- ad acqua del tipo automatico (sprinkler), esteso all’intera area produttiva e agli ambienti comunicanti, e manuale (idranti, estintori), per il resto dell’edificio;
- automatico a gas inerte, per il solo locale CED.
Gli impianti a idranti e sprinkler sono alimentati da una riserva idrica comune, costituita da un serbatoio esterno (capacità 500 m3) con 2 stazioni di pressurizzazione distinte e indipendenti (elettropompa, motopompa, pompa jockey) più predisposizione per un’ulteriore stazione.
La distribuzione è generalmente realizzata con tubi in pe-ad e in acciaio, con idranti soprassuolo posati esternamente al fabbricato. L’aria compressa è utilizzata prevalentemente per scopi produttivi. Il processo prevede separazione di condensa in serbatoio, filtrazione con filtro a cartuccia, essiccamento mediante circuito frigorifero (economizzatore aria–aria, evaporatore freon–aria, compressore ermetico, separazione e scarico condensa) e filtrazione finale con filtri a cartuccia, con raccolta della condensa durante le diverse fasi e separazione dell’olio.
Il compressore volumetrico rotativo esistente è stato riutilizzato come riserva del nuovo compressore, della medesima tipologia, composto da gruppi:
- di aspirazione con filtro e valvola di parzializzazione/vuoto;
- pompante di tipo bivite con separatore d’olio e relativo refrigerante;
- refrigerante finale con batteria aria-aria compressa, più separatore e scaricatore di condensa;
- di mandata, con valvole di ritegno e sezionamento, giunto antivibrante, manometri, pressostati e trasduttori di pressione.
La nuova unità dispone di uno scambiatore di calore acqua-olio, per il recupero e il trasferimento del calore sviluppato durante la compressione dell’aria, utilizzato per la produzione dell’ACS. La distribuzione dell’aria compressa avviene mediante reti ad anello in tubazioni d’acciaio inox, con calate dotate di attacchi rapidi valvolati.
Il sistema e la rete
Conforme UNI EN ISO 16484-5, il BACS/BMS è concepito per assicurare interoperabilità tra gli impianti (meccanici, elettrici ed elettronici di sicurezza) ed espandibilità attraverso un’architettura aperta, composta da supervisore generale dotato di interfaccia web multiutente, infrastruttura di comunicazione generale e bus di campo.
Fra le funzioni previste si distinguono:
- possibilità di configurazione di tutti i parametri dei regolatori di zona e delle apparecchiature connessi alla rete, con permessi alle operazioni in base al tipo di utente (utilizzatore/gestore/manutentore);
- gestione degli orari di funzionamento delle varie zone;
- gestione di accensione, parzializzazione e spegnimento degli impianti di illuminazione interna ed esterna, con stato di ogni singola lampada e diagnostica centralizzata dell’illuminazione di sicurezza;
- gestione degli allarmi per qualsiasi tipo di impianti (meccanici, elettrici, allarme incendio ecc..), e invio via e-mail degli stessi ai manutentori specifici;
- storicizzazione delle misure e degli stati/parametri acquisiti e impostati con creazione di relativi grafici e tabelle;
- misure energetiche e dei consumi con suddivisione per zone e impianti, con calcolo dell’efficienza e dei rendimenti dei generatori, archiviazione dei dati e creazione di report
- controllo dei serramenti motorizzati.
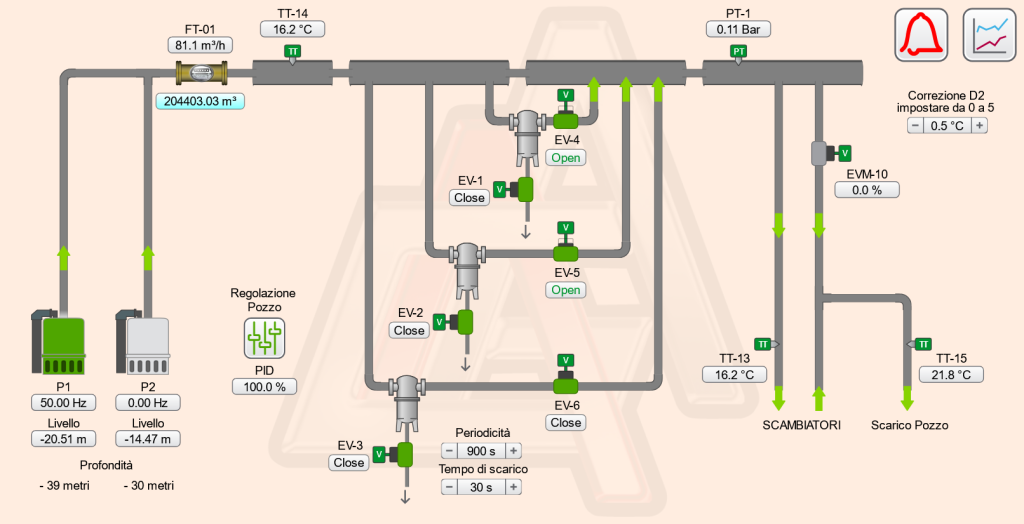
L’infrastruttura generale è basata su server (a bordo di macchine virtuali situate nel CED) connessi ai controllori di zona tramite la rete ethernet TCP/IP di stabilimento, dotata di collegamenti dorsali in fibra ottica (cablaggio strutturato) e switch evoluti in grado di gestire reti LAN virtuali e VPN.
I protocolli di trasmissione ammessi sono standardizzati e non proprietari (ad esempio BACnet/IP, MODbus/TCP, TVCC over IP).
L’infrastruttura periferica connette quella generale alle apparecchiature tramite bus di campo (KNX, DALI, MODbus, ZigBee ecc.) a partire dai quadri elettrici di zona. Le macchine con logica di regolazione a bordo (pompe di calore, ecc.) dispongono di punti di collegamento dedicati.
Gestione integrata delle informazioni
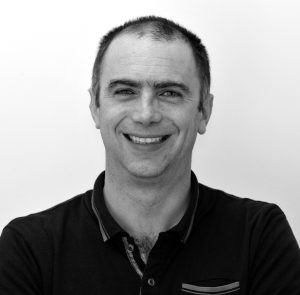
L’ing. Mario Ruatti è CEO e Direttore tecnico di T.E.S.I. Engineering: «Abbiamo sviluppato la progettazione fra la fine del 2021 e la metà del 2022, quando le demolizioni erano iniziate da pochi mesi. Dopo solo un anno, a metà 2023, il nuovo stabilimento era completo e funzionante. Dopo l’attivazione abbiamo impiegato ancora qualche mese per mettere a punto i dettagli, in stretta collaborazione con l’impresa installatrice».
Quali difficoltà avete incontrato e come sono state risolte?
«La progettazione non ha posto particolari problematiche: le tecnologie erano tutte conosciute e già utilizzate in progetti precedenti. Sapevamo che alcuni aspetti tecnici – ad esempio la taratura dei soffitti radianti – avrebbero comportato un impegno superiore. Abbiamo però affrontato altre complessità impreviste, legate principalmente all’integrazione tra gli impianti civili e quelli di processo.
D’intesa con la committenza è stata infatti realizzata un’unica rete di trasmissione dati, estendendo di fatto a tutte le funzioni i più elevati standard di sicurezza di tipo industriale. Alcune delle informazioni sul funzionamento degli impianti sono riservate ai servizi tecnici, che possono così operare senza interferenze nell’attività produttiva, ad esempio per la manutenzione periodica.
Altre informazioni sono invece condivise: uno dei principali vantaggi del sistema realizzato consiste nella possibilità di associare i dati di consumo energetico, rilevati dal monitoraggio, con quelli relativi alla produzione, ai fini della migliore gestione del processo industriale. Nonostante la più complessa messa a punto, ora lo stabilimento vanta un’efficienza energetica spettacolare».